In the critical world of product reliability and material science, environmental testing ensures components and assemblies can withstand real-world stresses. Two fundamental methods, thermal cycling and temperature cycling, are often mentioned. While both involve exposing materials to changing temperatures, they serve distinct purposes and employ different methodologies. Understanding the difference between thermal cycling and temperature cycling is essential for selecting the right test protocol. Central to both methods is the thermal cycling chamber, a sophisticated piece of equipment enabling precise temperature control.
What is Thermal Cycling?
Thermal cycling is an accelerated stress test designed to evaluate a material’s or component’s resilience to rapid and extreme temperature variations. The core objective is to induce thermal stress and fatigue, revealing potential failure points like cracking, delamination, or solder joint failure that occur due to the expansion and contraction mismatch of different materials.
The Thermal Cycling Process:
- Rapid Heating: The specimen inside the thermal cycling chamber is quickly heated to a predetermined high temperature (e.g., +125°C).
- Dwell at High Temp: The temperature is held for a short period to ensure thermal equilibrium.
- Rapid Cooling: The specimen is then rapidly cooled down to a predetermined low temperature (e.g., -40°C).
- Dwell at Low Temp: The temperature is held again briefly.
- Repetition: This sequence of rapid heating, dwell, rapid cooling, and dwell is repeated for hundreds or even thousands of cycles.
The thermal cycling chamber is crucial here, providing the precise control and speed necessary for these abrupt transitions, often achieving rates of 10°C/minute or higher.
Key Applications of Thermal Cycling:
- Electronics: Testing solder joint reliability (JEDEC standards), component fatigue (IC packages, PCBs), identifying “popcorning” in plastic packages.
- Aerospace & Defense: Evaluating avionics, satellite components, and materials exposed to extreme atmospheric temperature swings.
- Automotive: Assessing engine control units (ECUs), sensors, connectors, and under-hood components prone to rapid heating/cooling.
- Semiconductors: Accelerated life testing for chips and packaging.
- Materials Research: Studying fatigue life, crack propagation, and CTE (Coefficient of Thermal Expansion) mismatches.
What is Temperature Cycling?
Temperature cycling focuses on evaluating the long-term durability and reliability of materials and products under more gradual temperature variations that simulate real-world environmental exposure over time. The emphasis is on cumulative effects rather than rapid shock.
The Temperature Cycling Process:
- Controlled Transition: The specimen transitions from one temperature extreme to the other at a relatively slower, controlled rate.
- Extended Dwell Periods: The specimen is held at each temperature extreme (high and low) for a significantly longer period (hours or even days) compared to thermal cycling. This ensures the entire specimen reaches thermal equilibrium and experiences sustained stress.
- Repetition: This cycle of gradual transition and extended dwell is repeated for the required number of cycles or duration.
While often performed in the same type of equipment, a thermal cycling chamber used for temperature cycling tests is configured for slower ramp rates and longer dwells to accurately simulate these conditions.
Key Applications of Temperature Cycling:
- Consumer Electronics: Testing laptops, smartphones, wearables for performance and reliability under typical user environment variations (seasonal changes, day/night cycles).
- Automotive: Assessing interior components (dashboards, displays), lighting, and systems expected to endure slower seasonal temperature shifts.
- Building Materials: Evaluating seals, gaskets, windows, and structural components for durability against daily and seasonal temperature fluctuations.
- Medical Devices: Ensuring reliability of equipment stored or used in environments with varying temperatures.
- Packaging: Testing the resilience of packaging materials to temperature changes during shipping and storage.
Key Differences Between Thermal Cycling and Temperature Cycling
While both leverage thermal cycling chambers, their core distinctions lie in purpose, execution, and application:
Feature | Thermal Cycling | Temperature Cycling |
---|---|---|
Primary Goal | Induce rapid thermal stress & fatigue; find sudden failure points (cracks, solder fractures). | Simulate long-term environmental exposure; assess cumulative degradation over time. |
Rate of Change | Rapid transitions (e.g., >10°C/min). Simulates abrupt thermal shock. | Gradual transitions (e.g., <5°C/min, often slower). Simulates natural environmental changes. |
Dwell Times | Short dwell periods (minutes). Focus is on the stress of the transition. | Extended dwell periods (hours/days). Focus is on stress sustained at extremes and material creep/relaxation. |
Stress Induced | Primarily Thermo-Mechanical Stress (due to CTE mismatch during rapid expansion/contraction). | Thermal Stress combined with potential effects of time-dependent phenomena (creep, material aging, moisture diffusion). |
Typical Applications | Electronics (solder joints, packages), Aerospace components (rapid ascent/descent), Automotive under-hood. | Consumer electronics (longevity), Automotive interiors, Building materials, Packaging, Long-term storage. |
Chamber Focus | Optimized for high ramp rates and precision at extremes. | Optimized for stability during long dwells and controlled slower transitions. |
Conclusion: Choosing the Right Test
Selecting between thermal cycling and temperature cycling hinges on the specific failure mechanisms you need to uncover and the real-world conditions your product will face.
- Use Thermal Cycling (performed in a specialized thermal cycling chamber) when you need to rapidly identify weaknesses caused by sudden, extreme temperature shocks and thermal fatigue. It’s ideal for components experiencing quick power cycling, exposure to harsh environments like aerospace, or where CTE mismatch is a major concern.
- Use Temperature Cycling when you need to evaluate the long-term reliability and durability of products or materials exposed to slower, cyclic environmental temperature changes over their expected lifespan, such as consumer goods, building components, or items in storage.
Both methods are indispensable tools in the reliability engineer’s arsenal. The advanced capabilities of modern thermal cycling chambers make it possible to accurately perform both types of tests, ensuring products meet stringent quality and durability standards before reaching the market.
Need precision thermal testing? Explore how our advanced Rapid Thermal Cycling Chambers can meet your rigorous thermal cycling and temperature cycling requirements. Contact our experts today at zhy@szbonad.com.
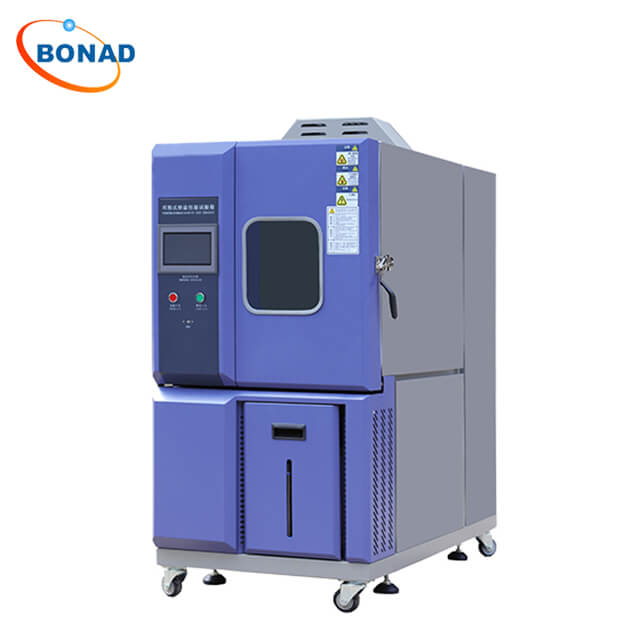