Why Salt Spray Testing is Non-Negotiable for Paints and Coatings
Corrosion costs industries billions annually. Salt spray testing (SST) is the frontline defense, simulating harsh environments to validate the durability of paints and coatings before real-world exposure. From automotive panels to marine equipment, SST ensures products withstand corrosive elements like saltwater, humidity, and pollutants.
How Salt Spray Testing Works: Science Meets Standards
- Corrosion Simulation
- Test chambers create a fine saltwater mist (5% NaCl solution) at 35°C and 95–98% humidity, accelerating oxidation.
- Advanced cycles combine UV exposure, drying, and SO₂ gas to replicate years of decay in days.
- Performance metrics: Gloss retention, adhesion strength, blistering, and rust progression.
- Key Standards & Protocols
- ASTM B117/ISO 9227: Govern test parameters (temperature, spray consistency, pH levels).
- Cyclic Tests (e.g., GM 9540P): Mimic dynamic environments (e.g., coastal air, de-iced roads).
BONAD’s Salt Spray Test Chamber: Precision Engineering
Feature | Technical Advantage |
---|---|
Temperature Control | ±0.5°C accuracy (ambient to 60°C) |
Cyclic Testing | Customizable wet/dry/UV/SO₂ cycles |
Spray System | Adjustable tower with calibrated 1–2 ml/hr/cm² sedimentation |
Safety | Over-temperature, dry-combustion & leakage protection |
Compliance | ASTM B117, ISO 9227, JIS Z 2371 |
Chamber Sizes | 110L to 1600L (supports batch testing) |
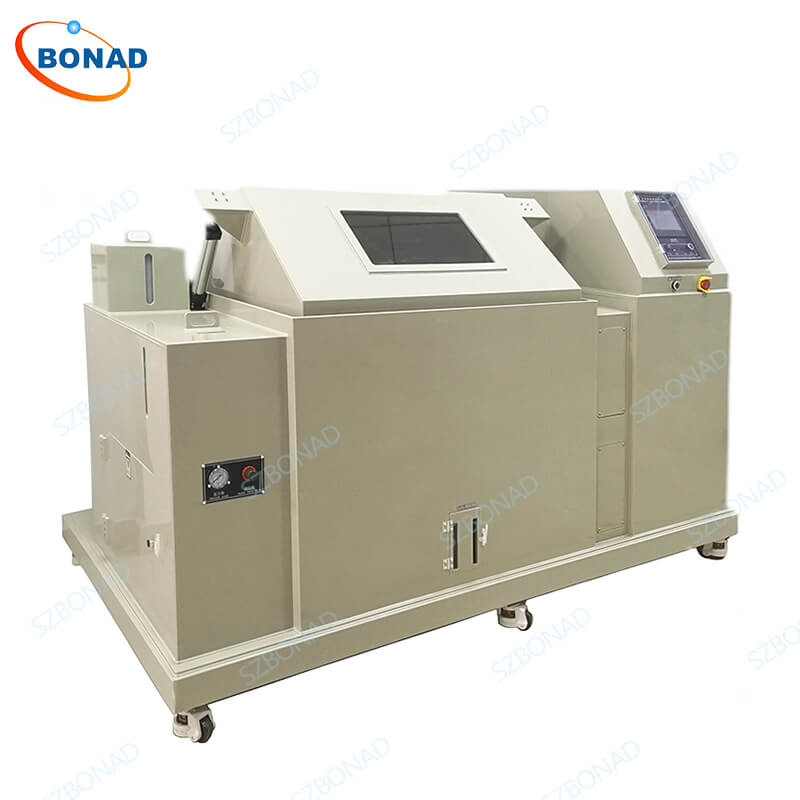
Industries Relying on SST
- Automotive: Prevents underbody corrosion.
- Aerospace: Ensures wing/fuselage coating integrity.
- Marine: Validates hull coatings against seawater.
- Electronics: Tests corrosion resistance of enclosures.
Benefits Beyond Compliance
- Durability Prediction: Identifies failure points (e.g., edge creep, blistering) early.
- Quality Control: 80% faster defect detection vs. field tests.
- Case Study: Nano-ceramic coatings passing 1,000-hour SST showed zero corrosion after 5 years in coastal zones.
Limitations & Complementary Tests
While SST excels in accelerated corrosion simulation, real-world factors (UV degradation, mechanical wear) require combined testing:
- Humidity Chambers: Assess moisture resistance.
- Cyclic Corrosion Tests: Simulate temperature/weather shifts.
- Field Exposure: Validates lab predictions (e.g., oceanfront testing sites).
Conclusion
Salt spray testing is indispensable for developing corrosion-resistant paints and coatings. BONAD Industry’s ASTM/ISO-compliant chambers deliver precise, repeatable results—ensuring your products exceed durability standards.
FAQ Section
Q: What’s the purpose of salt spray testing?
A: It evaluates corrosion resistance of coatings under accelerated salt-laden conditions, predicting real-world lifespan.
Q: How long does a typical test run?
A: Ranges from 24h (QC checks) to 1,000–2,000h (certification-grade validation).
Q: Which industries require SST?
A: Automotive, aerospace, marine, and electronics for corrosion-prone components.
Q: Can SST replace real-world testing?
A: No—it’s best paired with cyclic tests and field exposure for comprehensive validation.
Upgrade Your Testing Lab
Request a quote for BONAD’s salt spray test chambers at zhy@szbonad.com. ASTM B117-compliant | Customizable cycles | 24/7 support.