Why Dust Testing is Non-Negotiable for Automotive Reliability
Modern vehicles face relentless assault from dust, sand, and particulates. Dust test chambers are mission-critical tools, simulating harsh environments from deserts to construction sites to ensure components survive real-world abuse. By exposing parts to controlled particulate storms, manufacturers identify failure points early, enhance designs, and deliver vehicles that meet global reliability standards.
The Hidden Damage: How Dust Destroys Automotive Components
Microscopic Invasion: Particles (0.1-100μm) infiltrate seals, accumulating in electronics, bearings, and optics. This disrupts function and accelerates wear beyond design limits.
Electrical Failures: Conductive dust creates short circuits; non-conductive layers cause electronics to overheat by blocking heat dissipation.
Mechanical Destruction: Abrasive particles act like grinding paste in bearings and gears, increasing friction by up to 40% and slashing component lifespan.
Critical Components Demanding Rigorous Dust Testing:
- ECUs & Sensors: Engine controls, ADAS sensors, and airflow meters require IP6X sealing to prevent signal drift.
- Lighting & Optics: Headlights, cameras, and LiDAR must maintain optical clarity despite heavy dust buildup.
- HVAC Systems: Cabin air quality depends on filters and seals resisting clogging and contamination ingress.
Meeting Global Dust Resistance Standards:
- IP Ratings (IEC 60529): IP5X (dust-protected) and IP6X (dust-tight) are baseline requirements.
- Regional Mandates: EU (fine urban particulates), North America (coarse industrial dust), Asia (monsoon dust/humidity).
- Industry Benchmarks: SAE J575 (lighting), ISO 20653 (road vehicles), MIL-STD-810 (military extremes).
Simulating Real-World Hell: Advanced Chamber Capabilities
Modern dust chambers replicate extreme conditions with precision:
- Temperature: Ambient to 80°C (±0.5°C accuracy) for desert heat.
- Humidity: <30% RH for arid simulations.
- Particle Control: 0.1-100μm distribution (urban pollution to desert sand).
- Dynamic Cycling: Programmed sequences mimic day/night shifts and seasonal storms.
Proven Results: How Testing Boosts Durability
- Accelerated Aging: Compress years of damage into weeks of high-concentration testing.
- Failure Mode Analysis: Pinpoint design flaws in seals, materials, and thermal management.
- Design Optimization: Validate protective coatings, filtration, and sealing geometries before production.
Industry-Standard Testing Solutions: BONAD Chambers
BONAD Industry delivers automotive-grade dust test chambers engineered for reliability:
✅ Precision Control: 80°C temperature (±0.5°C), programmable particle concentration.
✅ Custom Configurations: 1-4m³ standard sizes, with bespoke dimensions and OEM-specific compliance.
✅ Full Support: Installation, training, 3-year warranty, and ongoing calibration (zhy@szbonad.com).
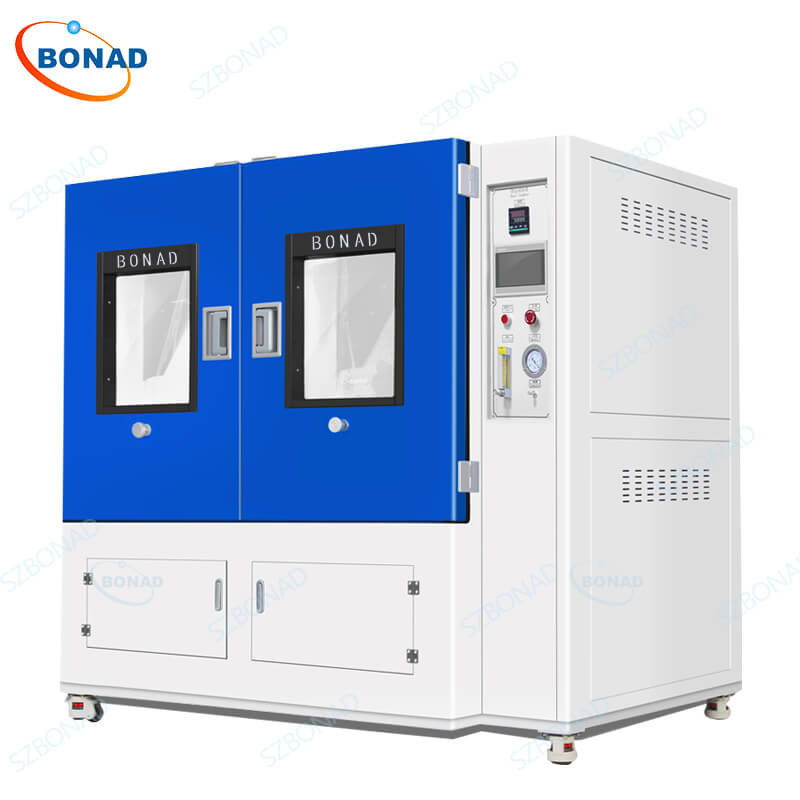
Conclusion
Dust test chambers are indispensable for automotive survival in harsh environments. They validate component resilience, ensure regulatory compliance, and prevent costly field failures. As vehicles grow more complex, rigorous dust testing isn’t optional—it’s foundational to brand trust.
FAQ
Q: What particle sizes are critical for automotive testing?
A: Test 0.1-100μm particles. Fine dust (0.1-10μm) mimics pollution; coarse sand (10-100μm) replicates deserts/construction sites.
Q: How long do dust tests typically run?
A: From 8 hours (basic IP checks) to several weeks for accelerated lifecycle validation, depending on component criticality.
Q: Can chambers simulate specific global regions?
A: Yes. Advanced chambers replicate desert (high temp, coarse sand), urban (fine particulates), or monsoon (dust + humidity) conditions.
Q: What standards require automotive dust testing?
A: Key mandates include ISO 20653, SAE J575, IEC 60529 (IP ratings), and OEM-specific protocols like Ford or Toyota specs.