Reliability testing is essential for assessing how a product performs throughout its intended lifespan under real-world conditions like use, transport, and storage. Key reliability tests include aging tests, salt spray tests, high/low temperature tests, and liquid resistance tests. Among these, aging tests are crucial for evaluating how materials degrade over time under specific environmental stresses.
What is an Aging Test?
Simply put, an aging test places a product in a controlled environment (like an aging chamber) for a set duration to observe changes before and after exposure. It simulates long-term effects in a shorter timeframe. Common aging tests are UV Aging, Xenon Lamp Aging, Ozone Aging, and Hot Air Aging. These tests are vital for materials like rubber, plastics, adhesives, coatings, and even metals.
UV Aging vs. Xenon Lamp Aging: Simulating Sunlight Damage
Both UV and Xenon lamp aging use specialized chambers to mimic sunlight, but they differ significantly:
Feature | UV Aging Test | Xenon Lamp Aging Test |
---|---|---|
Simulates | Primarily UV radiation damage | Full sunlight spectrum (UV + Visible + IR) |
Focus | Resistance to UV degradation | Overall weathering under full solar radiation |
Light Source | 8 x 40W UV fluorescent lamps | Xenon arc lamps |
Best For | Non-metallic materials (plastics, coatings) | Materials needing full-spectrum simulation (paints, textiles, plastics) |
Key Standards | • ASTM G154 • ISO 4892-1 • SAE J2020 • JIS D 0205 | • ASTM G155 • ISO 4892-1 • ASTM G151 • IEC 68-2-9 |
Key Insight:
“UV aging targets UV-specific damage, while xenon lamp aging replicates the complete solar spectrum for broader weathering assessment.”
Ozone Aging vs. Hot Air Aging: Testing Environmental Resistance
These tests evaluate material stability under gas exposure or thermal stress:
Feature | Ozone Aging Test | Hot Air Aging Test |
---|---|---|
Simulates | Exposure to ozone gas (e.g., industrial areas) | Long-term exposure to high temperatures |
Focus | Cracking/deg. from ozone reaction | Thermal oxidation & material hardening |
Best For | Rubber, elastomers, seals | Polymers, rubber, adhesives, electrical parts |
Key Standards | • ASTM D1149 • ISO 1431-1 • GB/T 7762 • JIS K 6259 | • ASTM D573 • ISO 188 • ASTM D3045 • IEC 60216-1 |
Material-Specific Testing:
- Rubber/Plastics: Often use Xenon Lamp + Hot Air Aging.
- Coatings: Primarily Xenon Lamp; UV Aging for coastal applications.
- Adhesives: Commonly rely on Hot Air Aging.
Essential Aging Test Equipment
To perform these tests, specialized chambers are required:
- UV Aging Test Chamber: For UV-specific degradation (e.g., QUV tester).
- Xenon Arc Test Chamber: For full-spectrum solar simulation.
- Ozone Aging Chamber: For controlled ozone exposure.
- Hot Air Oven: For thermal aging studies.
Choosing the Right Aging Test
Selecting the appropriate test depends on:
- Material Type (rubber, plastic, coating, metal).
- End-Use Environment (outdoor sunlight, ozone-rich areas, high heat).
- Relevant Industry Standards (e.g., automotive SAE J2020, electrical IEC 60216).
Pro Tip: Combine tests (e.g., Xenon + Hot Air) for materials facing multiple environmental stresses.
Key Aging Test Standards Summary
Test Type | Primary Standards |
---|---|
UV Aging | ASTM G154, ISO 4892-1, SAE J2020, JIS D 0205 |
Xenon Lamp Aging | ASTM G155, ASTM G151, ISO 4892-1, IEC 68-2-9 |
Ozone Aging | ASTM D1149, ISO 1431-1, GB/T 7762, JIS K 6259 |
Hot Air Aging | ASTM D573, ASTM D3045, ISO 188, IEC 60216-1 |
Conclusion
Understanding aging test standards (UV, Xenon, Ozone, Hot Air) is critical for ensuring product durability and compliance. By selecting the right test based on material, environment, and industry requirements (ASTM, ISO, IEC, JIS), manufacturers can accurately predict product lifespan and prevent field failures. Partner with certified testing labs and invest in appropriate aging chambers to validate your product’s reliability.
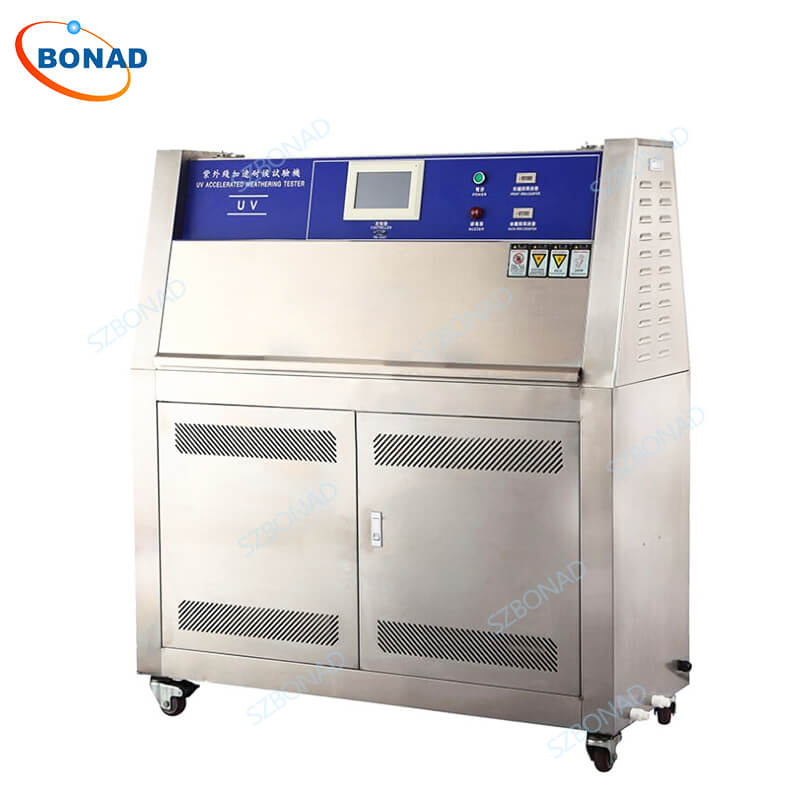