Achieving and maintaining stable humidity levels within benchtop humidity chambers is fundamental for reliable environmental testing across pharmaceuticals, electronics, materials science, and automotive industries. Fluctuations in Relative Humidity (RH) can compromise test validity, lead to non-compliance, and incur costly retesting. This guide details the critical practices for ensuring consistent RH performance between 10% and 98%.
Why Humidity Stability is Non-Negotiable in Testing
- Accuracy in Material Assessment: Minor RH variations dramatically alter material properties (e.g., hygroscopic electronics), leading to unreliable data and flawed product decisions. Stability ensures reproducible, real-world simulations.
- Regulatory Compliance (ISO 554, ASTM D618): Pharmaceutical stability studies, automotive component testing, and material evaluations mandate strict humidity tolerances. Documented stability is essential for regulatory approval.
- Economic Impact: Unstable conditions cause failed tests, costly repetitions, delayed timelines, material waste, and increased labor. Reliable chambers prevent these losses and accelerate time-to-market.
Top Causes of Humidity Fluctuations
Understanding instability sources is the first step to control:
- Temperature Interference: The primary culprit. Temperature changes directly impact RH (even with constant moisture). External variations, poor insulation, or internal heat sources create destabilizing gradients.
- Water Supply Issues: Impurities (minerals, organics) cause scale buildup, irregular steam output, sensor inaccuracy, and biofilms, severely degrading humidification performance and chamber integrity.
- Mechanical Degradation: Aging humidifiers/dehumidifiers, worn seals (allowing moisture leaks), and failing sensors or circulation fans reduce precision, cause drift, and create non-uniform humidity zones.
Optimizing Humidification & Dehumidification Control
Precise control balances moisture addition and removal:
- Steam Humidification (Best for High RH): Use purified water (distilled/deionized). Optimize via precise heater control, strategic nozzle placement, condensation management, and regular descaling. (±2% RH, 2-5 min response).
- Advanced Dehumidification:
- Refrigeration: Cools air below dew point for condensation. Effective for moderate-low RH (±1.5% RH, 3-8 min).
- Desiccant Absorption: Essential for ultra-low RH. Uses moisture-absorbing materials, often with regeneration (±3% RH, 10-15 min).
- Combined Systems: Offer highest precision (±1% RH, 1-3 min) for demanding applications.
- PID Control Algorithms: Modern chambers use Proportional-Integral-Derivative controllers. They continuously analyze sensor data, making real-time adjustments to humidification/dehumidification based on current error, past trends, and predicted future states to eliminate oscillations and ensure smooth transitions.
Humidity Control Method Comparison:
Control Method | Response Time | Accuracy Range | Best Application |
---|---|---|---|
Steam Humidification | 2-5 minutes | ±2% RH | High humidity requirements |
Refrigeration Dehumid. | 3-8 minutes | ±1.5% RH | Moderate to low humidity |
Desiccant Absorption | 10-15 minutes | ±3% RH | Ultra-low humidity levels |
Combined System | 1-3 minutes | ±1% RH | Precision applications |
Pro Tips for Consistent Performance
- Monitor & Analyze: Use data logging (USB/Ethernet) to track trends. Analyze graphs on touchscreen controllers to spot early signs of drift or needed maintenance.
- Smart Chamber Loading: Avoid overloading. Ensure samples are spaced for optimal airflow. Consider the thermal mass of samples, as it impacts temperature (and thus RH) stability. Use appropriate racks.
- Standardize Protocols: Minimize door openings. Define pre-test conditioning times. Train staff on procedures to minimize environmental disruption during testing.
Recommended Operating Ranges:
Temperature Range | Recommended RH Range | Conditioning Time | Typical Applications |
---|---|---|---|
-40°C to 0°C | 20% – 85% RH | 60-120 minutes | Cold storage simulation |
0°C to 40°C | 10% – 98% RH | 30-90 minutes | Standard environmental testing |
40°C to 85°C | 10% – 85% RH | 45-120 minutes | Accelerated aging |
85°C to 150°C | 10% – 60% RH | 90-180 minutes | High-temperature stability testing |
Essential Maintenance Checklist for Long-Term Stability
A proactive schedule prevents downtime and ensures accuracy:
- Sensor Calibration (Monthly – CRITICAL): Verify against certified standards (saturated salts/humidity generators). Adjust control parameters. Include temperature sensors.
- Water System Maintenance (Bi-weekly – HIGH Impact): Clean reservoirs, descale steam generators, flush lines, replace water filters. Use high-purity water (Conductivity < 10 µS/cm).
- Mechanical Checks (Varies):
- Seal Inspection (Monthly): Check door gaskets for wear/leaks.
- Filter Replacement (Quarterly): Maintain airflow and purity.
- Fan Maintenance (As per manual): Lubricate bearings, clean blades.
- Refrigeration System (Annual/Semi-annual): Professional servicing.
- Control System Check (Weekly): Verify setpoints, alarms, and basic functionality.
Maintenance Impact Summary:
Maintenance Task | Frequency | Impact on Stability |
---|---|---|
Sensor Calibration | Monthly | Critical |
Water System Cleaning | Bi-weekly | High |
Seal Inspection | Monthly | High |
Control System Check | Weekly | Critical |
Filter Replacement | Quarterly | Moderate |
Precision Engineered Solutions: BONAD Benchtop Humidity Chambers
BONAD Industry designs chambers integrating advanced technology for unparalleled RH stability (10-98% RH) across a wide temperature range (-40°C to +150°C):
- Advanced Control: Intuitive touchscreen interfaces, programmable sequences, remote monitoring (Ethernet), and precise PID algorithms.
- Safety Focus: Critical for battery testing (Li-ion), featuring built-in lighting, abnormal condition detection, and automatic safety protocols.
- Research-Grade Precision: Engineered for reliability in electronics validation, pharma stability, materials testing, and automotive QA, ensuring uniformity and data integrity.
Conclusion
Stable humidity in your benchtop chamber is achievable through systematic calibration, optimized humidification/dehumidification control, meticulous environmental monitoring, and strict adherence to a preventive maintenance schedule. Investing in these practices and precision equipment like BONAD chambers guarantees reliable test results, regulatory compliance, reduced operational costs, and accelerated product development cycles.
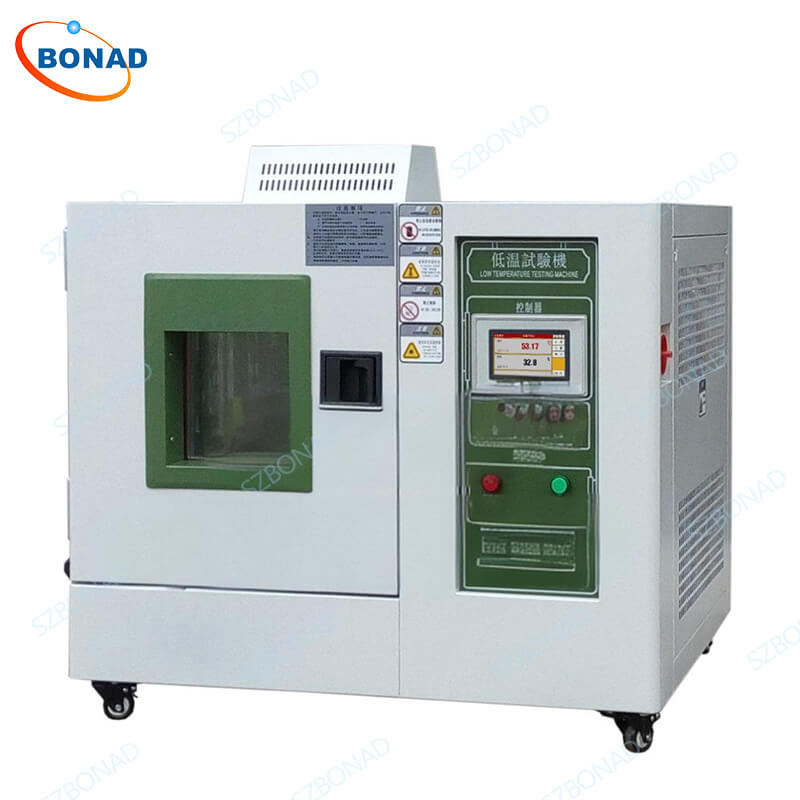
FAQ: Benchtop Humidity Chamber Stability
How often should I calibrate the humidity sensors?
Calibrate sensors monthly using certified reference standards. Increase frequency for high-usage chambers or critical precision applications.
What water quality is best for chamber humidification?
Always use distilled or deionized water with conductivity below 10 µS/cm. This prevents mineral scaling and contamination, ensuring optimal performance and reducing maintenance.
Can I test different materials together in one chamber?
Yes, but ensure adequate spacing between samples for proper airflow. Be mindful of potential material interactions (e.g., outgassing) that could affect humidity stability or cross-contaminate specimens.
Ready to achieve unmatched humidity control? Contact BONAD Industry today! Our experts will help you select the perfect benchtop humidity chamber and provide support to ensure your testing success. Email us at zhy@szbonad.com for information and custom solutions.