How to Assess Vibration Test Chamber Performance for Reliable Results
Your vibration test chamber is critical for product validation, but its accuracy hinges on rigorous performance assessments. With the vibration testing market projected to reach $2.5 billion by 2033, ensuring your equipment meets evolving standards is non-negotiable. This guide breaks down key metrics, calibration protocols, and troubleshooting strategies to maintain peak performance.
Why Regular Assessment Matters
Routine evaluations boost diagnostic accuracy by 20-30%, as operator experience grows and systematic checks identify drift. Data shows:
- Neurothesiometers achieve 0.52–0.78 К reliability with repeated tests.
- VSA-3000 systems gain reliability through consistent use.
- BONAD chambers enhance precision via multi-sensor data fusion and robust control systems.
Core Performance Metrics
Evaluate these parameters to validate your chamber:
Metric | Role in Testing | Optimal Control Method |
---|---|---|
Frequency/Amplitude | Simulates real-world stress profiles | BONAD’s ±0.5 Hz accuracy |
Acceleration | Measures rate of velocity change (m/s²) | Cross-verified sensor arrays |
Uniformity | Ensures even vibration distribution | Advanced feedback mechanisms |
Reliability | Maintains integrity under prolonged stress | 500+ hr durability validation |
Step-by-Step Calibration Protocol
- Sensor Mounting: Secure certified accelerometers using stud mounts (not wax).
- Signal Testing: Apply burst random signals across 5–2000 Hz; analyze via FFT.
- Validation: Compare outputs against reference sensors; document RMS errors.
- Environmental Control: Maintain ±1°C temperature stability during tests.
*Best Practice: Recalibrate every 6–12 months using ASTM/ISTA standards.*
Critical Troubleshooting Areas
- Noise Issues: Ground loops cause 40% of resonance masking → Shield cables and use isolated power.
- Sensor Errors: 50% RMS inaccuracies from poor mounting → Validate orientation and sensitivity.
- Load Imbalance: >30% amplitude deviation → Distribute weight evenly (max 500 kg for BONAD).
BONAD’s Engineering Edge
BONAD chambers resolve key pain points with:
- Triple-Environmental Testing: Combine vibration, temperature (-50°C to 150°C), and humidity (30–98% RH).
- Data Integrity: RS232/USB outputs for real-time PSD, transmissibility, and coherence tracking.
- Durability: SUS304 stainless steel interiors survive 1000+ test cycles.
Industry Application Insights
- Aerospace (35% market): Simulate takeoff vibration + thermal shock.
- Electronics (15%): Test PCB resilience under combined stressors.
- Automotive (25%): Validate component durability against road profiles.
FAQ: Quick Performance Checks
- Calibration frequency? Every 6–12 months.
- Critical metrics? Uniformity, PSD, and coherence >0.8.
- Sensor errors? Use EI/OED methods to optimize placement.
Partner for Precision
BONAD vibration test chambers deliver ISO-compliant accuracy for aerospace, automotive, and R&D sectors.
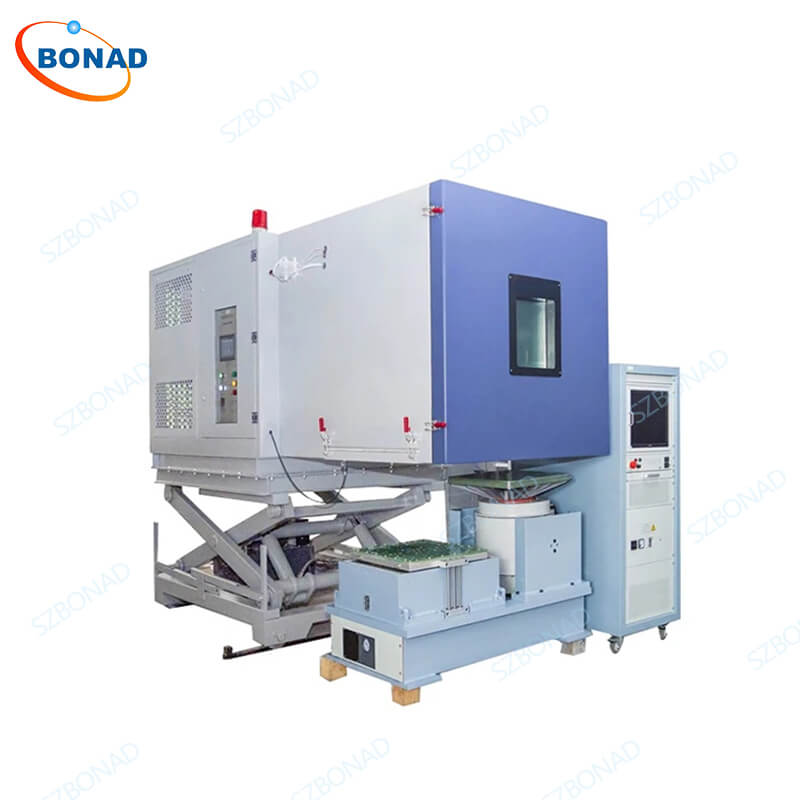