Sulfur Dioxide Corrosion Testing: Evaluating Material Resistance in Harsh Environments
Sulfur dioxide (SO₂) corrosion testing is a critical method for assessing how materials withstand corrosive SO₂-rich environments. Industrial materials—including steel, copper, aluminum, and protective coatings—are routinely exposed to SO₂ emissions from manufacturing, power generation, and urban pollution. Understanding SO₂ corrosion testing ensures optimal material selection, product longevity, and safety.
Why Test for Sulfur Dioxide Corrosion?
SO₂ is a colorless, pungent gas prevalent in industrial atmospheres. When oxidized, it forms sulfuric acid mist or sulfate aerosols that aggressively degrade exposed surfaces. Without proper testing, materials risk premature failure, leading to costly repairs or safety hazards.
Key Testing Methods
- Constant Temperature/Humidity Test
Samples are exposed to controlled SO₂ concentrations at fixed temperature/humidity levels. This simulates real-world conditions to observe corrosion rates. - Accelerated Corrosion Test
Uses elevated temperature, humidity, and SO₂ concentrations to speed up corrosion. Ideal for rapid material comparison and quality control.
4 Critical Best Practices
- Test Conditions: Tailor temperature, humidity, and SO₂ concentration to the material’s end-use environment (e.g., marine vs. industrial settings).
- Sample Preparation: Ensure samples are contamination-free, scratch-resistant, and representative of actual components.
- Real-Time Monitoring: Regularly inspect samples and document corrosion progression (e.g., weight loss, surface degradation).
- Analysis & Application: Translate test data into actionable insights for material selection, maintenance schedules, or coating improvements.
The Industrial Impact
SO₂ corrosion testing provides data-driven insights for:
- Selecting corrosion-resistant alloys/coatings
- Validating material performance in compliance with standards (e.g., ISO 6988, ASTM G87)
- Reducing lifecycle costs and downtime
Conclusion
Mastering sulfur dioxide corrosion testing is essential for industries operating in aggressive environments. By choosing the right method, adhering to strict protocols, and interpreting results accurately, engineers can enhance material durability and operational safety. As industrial emissions grow, advancing these testing methodologies remains vital for sustainable innovation.
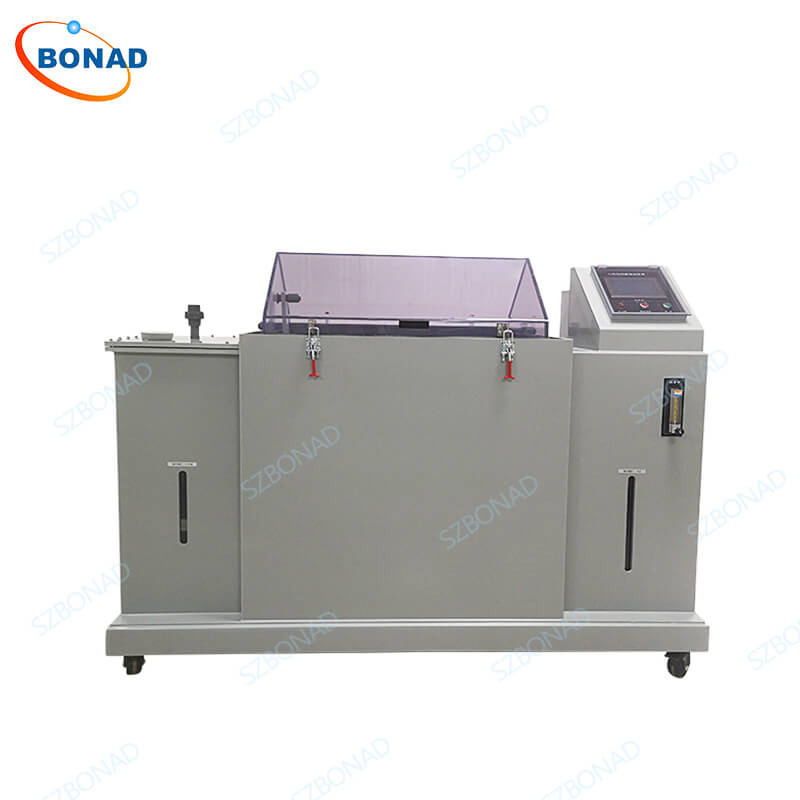