Vibration testing is a fundamental pillar of product development and quality assurance. Its core principle involves subjecting products or components to controlled, oscillating forces within a specialized vibration chamber. This simulates the real-world stresses encountered during transportation, operation, and handling. By replicating these dynamic conditions, engineers can proactively identify weaknesses, structural flaws, and potential failure points before products reach the market.
Why Vibration Testing Matters
Vibration testing is indispensable across critical industries:
- Automotive: Ensures engines, suspensions, and electronics withstand road vibrations.
- Aerospace: Validates structural integrity of aircraft and spacecraft components under flight stresses.
- Electronics: Tests resilience of circuit boards, connectors, and devices against handling and operational vibrations.
- Consumer Goods: Guarantees durability during shipping and everyday use.
Its primary goals are clear:
- Predict Failures: Uncover design flaws that could lead to malfunctions in real-world scenarios.
- Optimize Design: Enable manufacturers to refine products for peak reliability and performance, exceeding customer expectations.
This proactive approach reduces warranty costs, enhances brand reputation, mitigates failure risks, and ensures compliance with stringent industry standards.
How Vibration Chambers Simulate Reality
Vibration chambers are sophisticated labs replicating real-world dynamic stresses. Key components work in concert:
- Shaker Table: The core platform where the test specimen is mounted. It generates precise, controlled vibrations mimicking transportation, operation, or environmental exposure.
- Controller System: The “brain” regulating vibration parameters:
- Frequency: Cycles per second (Hz)
- Amplitude: Magnitude of movement (G or displacement)
- Duration: Test length
Ensures consistent, repeatable test conditions.
- Fixture Mechanism: Securely holds the specimen during intense testing, preventing slippage and ensuring accurate force transfer.
These chambers simulate diverse profiles:
- Sinusoidal Waves: Test resonance frequencies and fatigue life.
- Random Vibrations: Replicate the complex, unpredictable motions of real-world environments (e.g., rough roads, turbulent flight).
The Vibration Testing Process: Key Steps
A structured approach ensures reliable results:
- Test Plan Development: Define objectives, specific test conditions (profile, levels, duration), and clear pass/fail criteria.
- Test Specimen Preparation: Mount the product securely onto the shaker table using appropriate fixtures, replicating its operational orientation.
- Test Execution: Program the chamber controller with the desired vibration profile. Initiate the test while continuously monitoring the specimen for performance issues or failures.
- Data Collection & Analysis: Record critical data (acceleration, displacement, stress). Analyze results to pinpoint weaknesses, resonance frequencies, and performance thresholds.
- Reporting & Documentation: Generate a detailed report summarizing the test setup, conditions, results, analysis, and any observed failures – crucial for design improvements and QA.
Key Benefits of Vibration Testing for Manufacturers
Investing in vibration testing delivers significant returns:
- Enhanced Product Reliability: Identify and fix weaknesses early, leading to more durable, longer-lasting products.
- Substantial Cost Savings: Prevent expensive recalls, warranty claims, and field failures by catching issues in the lab.
- Guaranteed Compliance: Meet critical industry standards (MIL-STD, IEC, ASTM, SAE, ISTA) and regulatory requirements efficiently.
- Increased Customer Satisfaction: Deliver robust products that perform flawlessly under stress, building trust and brand loyalty.
- Reduced Time-to-Market: Streamline validation and avoid costly late-stage design changes.
Conclusion: The Foundation of Robust Product Design
Vibration testing, grounded in the principle of simulating real-world oscillatory forces, is non-negotiable for developing reliable, high-quality products. By leveraging advanced vibration chambers and a rigorous testing process, manufacturers gain invaluable insights, drive innovation, reduce costs, and ensure customer satisfaction. It transforms uncertainty into engineered resilience.
Ready to enhance your product’s reliability? Contact our experts at zhy@szbonad.com to discuss your vibration testing requirements and discover the right chamber solution for your needs.
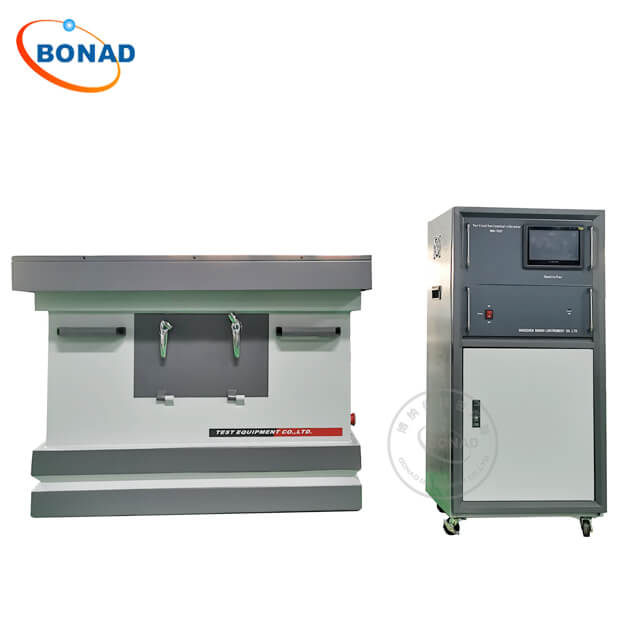