Thermal shock chambers are indispensable tools across critical industries like electronics, automotive, aerospace, and materials science. They rigorously test product durability by simulating sudden, extreme temperature shifts – replicating real-world stresses from desert heat to arctic cold. Understanding how these chambers operate is key to ensuring product reliability and safety.
What is a Thermal Shock Chamber?
A thermal shock chamber is specialized testing equipment designed to rapidly expose materials and products to alternating extreme high and low temperatures. This process evaluates how well components withstand thermal stress, identifying potential failures before products reach the market.
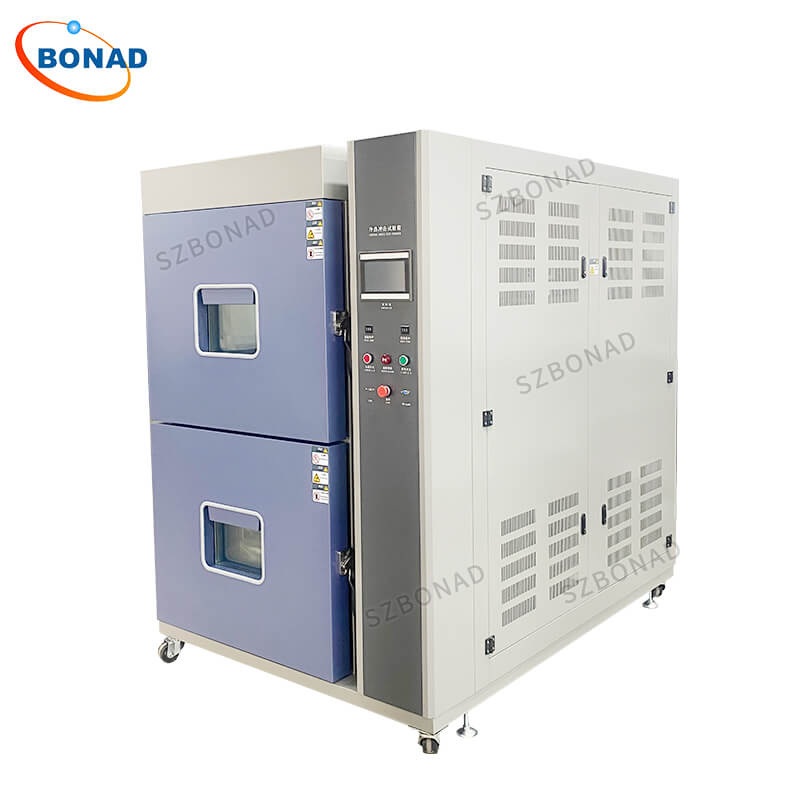
Core Components Enabling Rapid Transitions
- Dual-Zone System: Features separate, precisely controlled Hot and Cold zones for instant temperature switching.
- Precision Control System: Advanced programmable controllers maintain exact temperatures and automate test cycles for repeatable results.
- Robust Cooling & Heating: Achieves extremes using liquid nitrogen/mechanical refrigeration for cold and electric heaters for rapid heating.
- High-Speed Transfer Mechanism: Instantly moves test specimens between zones, minimizing transition time for maximum thermal shock effect.
How Does a Thermal Shock Chamber Work? (Step-by-Step)
- Specimen Placement: The test sample is loaded into either the hot or cold zone based on the test protocol.
- Temperature Regulation: Sophisticated controls rapidly achieve and maintain the target extreme temperature (e.g., +150°C or -65°C).
- Dwell & Stabilization: The specimen remains in the initial zone until its temperature fully stabilizes.
- Rapid Transfer: The transfer mechanism swiftly moves the specimen to the opposite extreme zone (< 10 seconds typical), creating intense thermal shock.
- Repeat Cycles: Steps 2-4 repeat for a specified number of cycles or duration, continuously stressing the specimen.
- Analysis: Engineers evaluate the specimen for failures (cracks, delamination, electrical faults) to assess resilience.
Key Industry Applications
- Electronics & Semiconductors: Testing PCBs, ICs, solder joints, and connectors for failures caused by power cycling or environmental shifts.
- Automotive: Validating engines, sensors, ECUs, lighting, and materials against temperature swings from winter cold to engine bay heat.
- Aerospace & Defense: Ensuring avionics, satellite components, and structural materials survive rapid altitude/temperature changes.
- Materials Science: Researching metal fatigue, plastic brittleness, ceramic cracking, and composite delamination under thermal stress.
Critical Benefits for Manufacturers
- Enhanced Product Reliability: Uncovers design weaknesses and failure points early in development.
- Accelerated Life Testing: Simulates years of thermal stress in days/weeks, speeding time-to-market.
- Regulatory Compliance: Meets stringent industry standards (MIL-STD, IEC, JEDEC, ISO 16750).
- Cost Reduction: Prevents expensive recalls, warranty claims, and brand damage by catching flaws pre-production.
- Quality Assurance: Ensures products perform reliably in real-world environments, building customer trust.
Conclusion
Thermal shock chambers are vital for engineering robust, reliable products. By simulating extreme and rapid temperature transitions, they expose potential failures, drive design improvements, and ensure components meet the highest standards of durability. Investing in thermal shock testing is crucial for product success in demanding environments.
Ready to Ensure Your Product’s Thermal Resilience?
Contact our testing experts today at zhy@szbonad.com to discuss your thermal shock testing requirements and find the right chamber solution.